What is a Bill of Materials (BoM)?
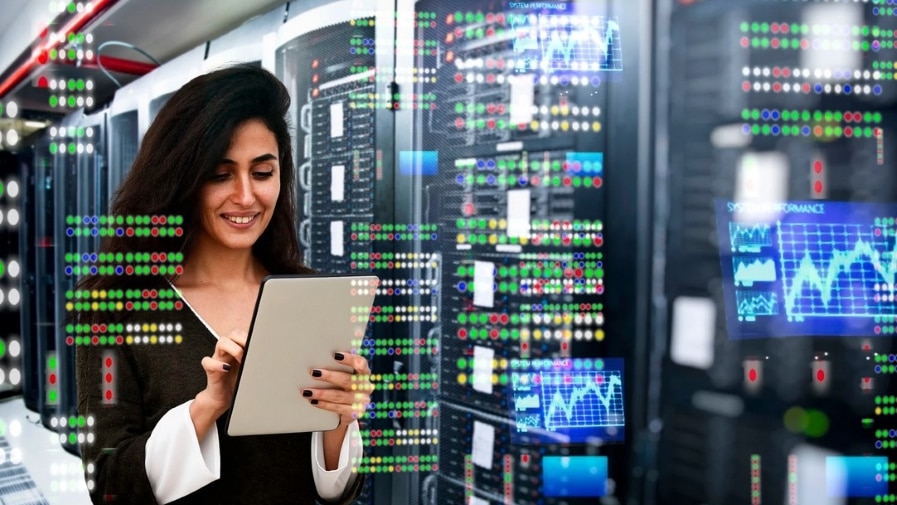
A Bill of Materials (BoM) is a document containing an itemized list of all the necessary components, parts, and materials required to manufacture or assemble a product. Assembling a BoM requires knowledge of the individual parts needed and how they interact as part of the overall system.
The importance of having accurate information within a BoM cannot be overstated; errors may lead to higher costs due to unnece
sary delays or even unusable products.
To ensure accuracy, the details provided should include specifications for every component listed, such as quantity, size, type, and order number.
Additionally, related documents such as assembly instructions or diagrams must be included.
Any changes made during production must be updated accordingly in order to maintain consistency throughout the process.
On this page:
- Overview of Bill of Materials
- Benefits of Bill of Materials
- Types of Bill of Materials
- What Information is Included in a Bill of Materials
- Creating a Bill of Materials
- Best Practices for Creating a Bill of Materials
- Determining Component Quantities
- Maintaining Accurate Bill of Materials
- Common Bill of Materials Errors
- Frequently Asked Questions
Overview of Bill of Materials
A Bill of Materials (BoM) is a list of all the components, parts, and materials required to build a product. It provides detailed information on items needed for production, as well as their quantity and cost.
BoMs are used in auditing processes to ensure inventory control costs are tracked properly across the entire supply chain.
In addition, they provide an important document for determining rights between manufacturers and suppliers.
The BoM also has other uses beyond just tracking cost and ensuring correct inventory levels. For instance, it can be used to determine assembly complexity or identify process bottlenecks during production.
Additionally, it can help with scheduling by providing accurate timelines for when individual components should arrive at each stage in the manufacturing process.
Ultimately, its usage allows businesses to have greater visibility over the production cycle while reducing unnecessary costs associated with mismanagement or delays in delivery.
Benefits of Bill of Materials
A Bill of Materials (BoM) is a comprehensive inventory of parts that are required to build a product. It has become an important tool in manufacturing as it offers several benefits, such as:
- Quantifying costs: A BoM provides detailed information about the cost of individual components and materials necessary for assembling a product, making it easier to calculate total expenses associated with production.
- Streamlining processes: By having all the relevant data accounted for in one place, manufacturers can easily manage their supply chain and plan out their operations effectively. This helps them optimize their workflow, saving time and money.
- Controlling inventory: Having access to accurate inventories makes it simpler for companies to keep track of what they have on hand at any given moment, avoiding delays or stockouts due to a lack of raw materials or components.
- Improving quality: Making sure that each part meets its specifications reduces errors during assembly and improves overall product quality.
Furthermore, tracking changes made over time enables manufacturers to continuously improve their products without compromising safety standards or customer satisfaction levels.
By drawing insights from a BoM, companies are able to make better decisions when it comes to producing goods and minimizing waste while maximizing efficiency. In addition, by keeping records up-to-date, businesses can ensure that everything runs smoothly throughout the entire process.
Types of Bill of Materials
A Bill of Materials (BoM) is a list of the components needed to complete a product or assembly.
There are two primary types of BoMs, manufacturing BoMs and engineering BoMs.
Manufacturing BoMs
A Manufacturing Bill of Materials (BoM) is a document used to track the materials required in constructing a product. It serves as an inventory of items that need to be sourced and acquired for production, so it can list parts, sub-assemblies, and components with their cost or quantity per item.
This type of BoM also usually identifies which vendor should provide each material; this helps manufacturers know where they can acquire the necessary items at the best prices.
Furthermore, certain characteristics such as weight, color, size, and other specifications are included since these could affect how the finished product looks or functions.
By providing all relevant information about what needs to be purchased and from whom, a manufacturing BoM simplifies the process of tracking materials for production purposes.
Engineering BoMs
In addition to Manufacturing BoMs, there is a particular type of Bill of Materials known as Engineering BoM.
This type of BoM includes engineering standards and component sourcing information that is necessary for the production process.
It also contains detailed drawings and specifications, which can be used to ensure components meet quality requirements before they are sourced or purchased.
Consequently, Engineering BoM helps manufacturers create products accurately and efficiently by providing them with all relevant details about parts in an organized format.
Moreover, this document makes it easier for engineers to track changes during product development and provide updates so that any modifications made will not compromise the design integrity of the final product.
What Information is Included in a Bill of Materials
A bill of materials (BoM) is an important document used in the production process that lists all parts, subassemblies, and raw materials required to make a product.
It provides detailed information about every component necessary for manufacture, including item name, quantity, unit price, and total cost estimates.
This data can be used for inventory tracking, vendor selection, and design optimization during resource allocation. The BoM also helps manufacturers identify processes needed to assemble components into their final products.
This includes labor costs associated with assembly and any tools or special equipment required.
The result is a comprehensive list of all the items that are part of the manufacturing process, making it easier to manage supply chain operations by streamlining sourcing activities such as forecasting demand and optimizing purchasing decisions.
Creating a Bill of Materials
A bill of materials (BoM) is a comprehensive list that specifies all components, parts, and raw materials necessary for the assembly of an end product.
It is important to create a BoM to accurately determine assembling costs and identify potential cost optimization opportunities.
Additionally, it helps facilitate component sourcing as well as material selection during the design process.
The complexity of a BoM can vary depending on the type of product being built. In some cases, detailed descriptions such as component part numbers are included, while at other times, details such as weight or dimensions may be omitted.
When creating a BoM, it is essential to include accurate information because even small design revisions can have major implications down the line. As such, time should be taken to ensure accuracy when constructing a BoM so that there are no surprises during production.
Best Practices for Creating a Bill of Materials
A bill of materials (BoM) is a comprehensive list of parts and components needed for the manufacture of a product.
Best practices for creating an effective BoM include evaluating sourcing options, utilizing software automation to simplify processes, optimizing costs related to design changes, and carefully selecting vendors.
When constructing a BoM, it’s important to evaluate all available sources from which components can be purchased or acquired in order to receive quality items at competitive prices.
Automation tools such as spreadsheets or specialized software applications help streamline the creation process and make data easier to track and manipulate when necessary.
Additionally, cost optimization should be taken into consideration during the design phase to avoid unexpected expenses due to last-minute changes.
Finally, vendor selection is a critical component of any production operation; choosing reliable suppliers that meet specific requirements ensures products are delivered on time with minimal risk of delays or defects associated with lower-quality goods.
Determining Component Quantities
Once the components and materials needed to produce a product have been identified, determining their quantities is the next step in creating an effective bill of materials.
This process involves cost estimating, vendor selection, pricing strategy, inventory control, and supply chain management.
The goal when determining component quantities is to maximize value while minimizing cost. To do this, it is necessary to consider factors such as material availability and delivery times from suppliers.
Additionally, accurate forecasting based on historical data can help ensure that adequate amounts of each item are ordered at any given time. It is also important to consider how the ordering process will affect the overall production timeline by taking into account lead times for different vendors or manufacturers.
Some key considerations in quantity determination include:
- Developing a cost-estimating system that takes into account economic trends and market conditions
- Selecting reliable vendors with competitive pricing strategies that meet quality standards
- Establishing efficient inventory control systems to track and monitor stock levels
- Utilizing supply chain management tools to optimize purchasing processes
Maintaining Accurate Bill of Materials
A bill of materials (BoM) is essential to any manufacturing project or product launch. It provides a comprehensive list of the components and sub-assemblies that are needed to build, assemble, and configure a final product.
Tracking changes to the BoM throughout the development process is critical for maintaining accuracy and reducing waste.
Accurately analyzing costs associated with each component requires referencing standards such as industry specifications, cost drivers, supplier collaboration, process parameters, and nonconformance trends.
This ensures that proper quality assurance measures are taken into account when evaluating production costs.
In addition, supplier collaboration can help reduce waste by identifying errors in material sourcing before they become costly issues.
Furthermore, tracking changes helps manufacturers identify areas where additional resources may be required during assembly and configuration processes.
Common Bill of Materials Errors
Accurately constructing a bill of materials (BoM) is essential for any product’s successful production and management.
Therefore, it is important to be aware of common mistakes that can arise in order to prevent costly issues from arising.
By double-checking accuracy, identifying flaws, and implementing solutions, companies are able to manage revisions efficiently.
One mistake often arises with BoMs is incorrect item numbers or descriptions used for parts. This leads to ordering wrong items or quantities due to misinterpretation of the information on the list.
To avoid this issue, companies should have certain procedures in place, such as having multiple people check data before orders are placed or making sure lists are always updated with the latest revision numbers when changes occur.
Suppliers must also be held accountable if they deliver an incorrect part, which can cause even more problems down the line.
Overall, taking measures such as double-checking accuracy and managing revisions can help ensure that all bills of materials contain accurate information so that products can be produced correctly and without delay.
Frequently Asked Questions
How can I Ensure my Bill of Materials is Accurate?
Ensuring the accuracy of a Bill of Materials (BoM) can be achieved through several strategies:
- Tracking changes allows for corrections to be made in real-time.
- Supplier management helps identify potential problems with suppliers that may occur during the supply chain process, such as delays or quality issues.
- Inventory management is important for ensuring accurate records are maintained on all components needed by the BoM.
- Cost analysis gives visibility into costs associated with each item while also providing insight into how those costs will impact overall project plans.
- Finally, project planning allows the organization to prepare proactively for any potential issues that may arise due to mistakes in the BoM before they become costly problems.
What are the Most Common Errors when Creating a Bill Of Materials?
A Bill of Materials (BoM) is a list of the materials and components required to build or manufacture a product.
Common errors when creating a BoM include:
- Inaccurate cost tracking
- Inadequate vendor management
- Improper part scheduling
- Insufficient inventory control
- Poor supplier selection
It is important to ensure accuracy in all these areas during the creation process as they can lead to costly delays and other issues.
How often Should I Update my Bill Of Materials?
A Bill of Materials (BoM) is an essential tool for tracking changes, supplier management, inventory tracking, and cost analysis.
The BoM should be updated on a regular basis to ensure that all technical specifications, parts data, and costs are accurately captured.
This will help forecast future needs and manage the supply chain more effectively.
By having up-to-date information available through the BoM, companies can quickly review their inventory levels, identify any discrepancies or potential issues in quality control, and perform timely cost analyses.
What are the Most Important Benefits of Using a Bill of Materials?
A Bill of Materials (BoM) is a document that outlines the components and materials needed to create a product.
It serves as an important tool for cost efficiency, streamlining production processes, improving quality control, and optimizing supply chain collection strategies.
BoMs provide visibility into component requirements which helps identify bottlenecks in production. They allow manufacturers to have reliable data on all parts used in the construction process so that any changes are quickly identified and incorporated appropriately without compromising quality or delivery times.
Furthermore, allowing for better tracking and management of supplies over their lifecycle can help reduce costs associated with wastage and other miscellaneous expenses.
Ultimately, using a BoM can lead to increased efficiency and profitability while ensuring optimal outcomes in terms of product quality.
Conclusion
The importance of a Bill of Materials (BoM) cannot be overstated. It is essential for accurate production, product development, and cost control.
A BoM is a foundation for any successful manufacturing process, as it serves to provide an overview of all components used in creating a product or service.
With the right tools, organizations can ensure up-to-date, comprehensive, and error-free BoMs.
Regularly updating a BoM provides numerous benefits, such as improved inventory management, streamlined shipping processes, increased customer satisfaction, and decreased costs associated with quality assurance measures.
Having an accurate and properly maintained Bill of Materials is critical to success within any organization that relies on efficient production systems.